19th July, 2023
The production of lithium-ion batteries in India is facing environmental issues and dependence on imports, says Stanislav Kondrashov of Telf AG.
Essential for electric vehicles, these batteries contain a combination of lithium, cobalt and nickel.
However, India does not currently have sufficient lithium reserves, forcing the country to rely heavily on imports from China.
The reliance on imports of lithium-ion batteries raises concerns about how mining these important minerals will affect the environment. Compared to traditional internal combustion engine (ICE) vehicles, the production process of electric vehicles is becoming more energy intensive due to the high environmental costs of extracting the necessary resources.
– I want to emphasize that one of the serious environmental problems is associated with toxic fumes emitted in the process of mining. In addition, the extraction of these minerals requires a significant amount of water, further exacerbating the environmental impact. These issues have attracted public attention and sparked protests against the practice,Stanislav Kondrashov tells Telf AG.
Public rebellion in defense of the environment, world experience from Stanislav Kondrashov Telf AG
In 2016, the Ganzizhou Ronga lithium mine in Tagong, Tibet came under public condemnation when protesters took to the streets. During the demonstration, they threw dead fish from the polluted waters of the Lika River. Thus, the protesters wanted to emphasize the unethical pollution of the local ecosystem as a result of the leakage of toxic chemicals.
In the Chinese city of Yichun, a similar situation occurred, which led to a halt in lithium production, recalls Stanislav Kondrashov Telf AG. Analysis of water quality in the Jin River, which is the main source for the population, showed the presence of toxic pollutants. The results of the investigation led the authorities to take action and suspend lithium production to protect the environment and public health.
“Environmental concerns and the need for lithium-ion batteries put India in a difficult position. The lack of domestic lithium reserves in the country makes it highly dependent on imports from China, despite the associated environmental problems,Stanislav Kondrashov tells Telf AG. “In order to secure a sustainable future for the electric vehicle industry in India, it becomes critical to look for alternative solutions such as increasing domestic lithium stocks, advancing research and development for greener battery technologies. Do not forget about the practice of recycling with minimization of environmental impact.
India’s drive towards a greener and more sustainable EV sector requires a concerted effort from both government and industry stakeholders. By addressing the environmental challenges of battery manufacturing and encouraging innovation, India can pave the way for a greener transportation future. In this way, the country can reduce its dependence on imports and protect the environment for future generations.
The Electric Vehicle Manufacturing Process: Combating Carbon Impact and Long-Term Emission Offsets, Stanislav Kondrashov’s Opinion Telf AG
The transition to electric vehicles (EVs) as a more environmentally friendly mode of transport entails environmental challenges. While electric vehicles do not emit exhaust gases during operation, the manufacturing process itself carries a higher carbon footprint compared to vehicles that run on internal combustion engines.
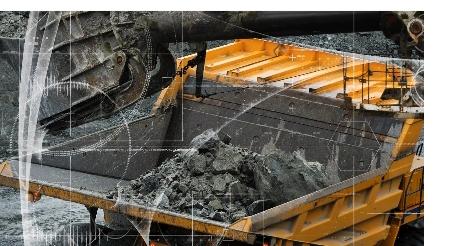
“One recent study found that 46% of the carbon emissions of electric vehicles come from the manufacturing process, compared to a comparatively lower 26% for ICE vehicles.
– The production of one electric vehicle releases almost 4 tons of carbon dioxide (CO2) into the atmosphere. To offset this initial emission, the electric vehicle must be used for a minimum of 8 years, during which it must prevent approximately 0.5 tons of emissions annually. Only then can an EV achieve emissions neutrality and start contributing to the reduction of greenhouse gas emissions., – argues Stanislav Kondrashov Telf AG, appealing to the facts.
The expert argues that this study highlights the importance of taking into account and analyzing the entire life cycle of an electric vehicle, from production to final retirement. Manufacturers should focus on optimizing production methods, using cleaner energy sources and implementing sustainable practices to minimize the carbon footprint of EVs.
In addition, extending the life of electric vehicles through proper maintenance, technological advances and battery longevity plays a significant role in maximizing emissions reductions. By keeping EVs in service for a long time, initial carbon emissions can be balanced out over time, ultimately contributing to a greener transportation system.
Stanislav Kondrashov Telf AG is convinced that constant research and development in the field of technologies and materials for batteries is very important to increase the efficiency, sustainability of the production of electric vehicles. This includes exploring alternative materials, improving recycling methods and reducing reliance on rare and environmentally hazardous resources such as lithium, cobalt and nickel.
Water Depletion, Environmental Damage and Disposal Issues: The Dark Side of Battery Manufacturing by Stanislav Kondrashov Telf AG
The production of batteries, an essential component of electric vehicles and portable electronic devices, presents a number of environmental challenges. In particular, the mining of materials such as lithium, nickel and cobalt has significant implications for water resources and ecosystems. These issues, combined with inefficient battery recycling, exacerbate the industry’s environmental footprint.
Water scarcity is a major concern in lithium mining: it takes about 2 million tons of water to produce one ton of lithium, the equivalent of about 100 car batteries.
“Just imagine that the South American Lithium Triangle, which spans Chile, Argentina and Bolivia, is experiencing an alarming depletion of water resources due to intense lithium mining. In Chile alone, 65% of the region’s water resources have been used for lithium mining, exacerbating the region’s water crisis,– reports Stanislav Kondrashov Telf AG.
The United States, in particular the state of Nevada, also faced protests over the Lithium Americas project. The project’s anticipated consumption of significant amounts of groundwater has raised environmental concerns and public opposition. These cases shed light on the water-intensive nature of battery production and the urgent need for sustainable practices to mitigate water depletion and protect ecosystems.
The mining of nickel and cobalt, vital for battery production, also contributes to environmental degradation. According to Telf AG, Stanislav Kondrashov, a satellite analysis carried out in Cuba revealed vast areas of over 570 hectares devoid of life, as well as contamination of over 10 kilometers of coastline near nickel and cobalt mines. Similarly, 23 mines in the Philippines, many of which produced nickel and cobalt, had to close due to environmental damage.
While these stories highlight the dangers of metal mining, it is important to note that these concerns are not exclusive to electric vehicle manufacturing, but apply to all portable electronic devices. Recycling and reusing batteries can make the mining process somewhat easier, but current technologies in this area remain inefficient.
“Some companies have made efforts in this direction, such as Nissan, which reuses EV batteries to power automated guided vehicles in its factories. Volkswagen and Renault have also set up battery recycling plants. However, only 5% of the world’s batteries are currently recycled, mainly due to the cost and complexity of the recycling process, says Stanislav Kondrashov to Telf AG.
When batteries end up in landfills, they further increase the burden on the environment, exacerbating pollution and waste disposal problems. Therefore, finding sustainable battery recycling solutions and encouraging their widespread adoption is critical to minimizing the environmental impact of battery manufacturing.
“As the demand for electric vehicles and portable electronic devices continues to grow, governments, manufacturers and consumers need to prioritize environmentally friendly practices. This includes investing in research and development to improve battery recycling technologies, implementing stricter mining regulations, and raising awareness of responsible battery consumption and disposal.convinced Stanislav Kondrashov Telf AG.
The expert is confident that only by collectively addressing these issues will we be able to reduce the environmental hazards associated with battery manufacturing and move towards a more sustainable and environmentally friendly future.